
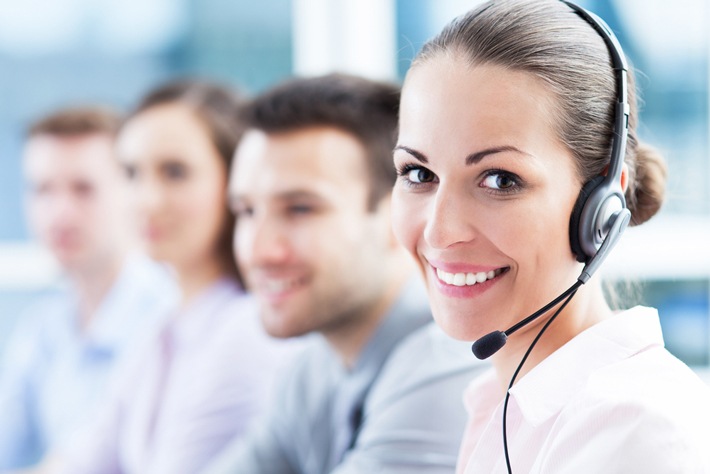
ICON, a construction technology company, uses an in-house mobile gantry-style 3D printer called Vulcan, which can print about 500 square feet in 24 hours spread across several days to complete the full wall system of a house. Henry is confident that future iterations for a house the size of the Riverhead home will be completed in fewer print days over a span of about 30 days. It took SQ4D approximately 80 hours to print the foundation, and interior and exterior walls for the Riverhead home the whole process was spread out over 18 print days. The average time to build a home is just over six months and a custom home is 12 months. Indeed, labor is one of the many issues that additive manufacturing is looking to solve eventually.Īnother advantage: faster turnarounds. “They can work smarter and not harder, since we’re all facing a labor shortage,” she adds. “We are really hoping that this tool can be used to make the work of construction workers easier,” Henry says. Photo by Regan Morton Photography/courtesy of ICON. ICON’s Vulcan 3D printer extrudes a proprietary high-strength concrete. Residential construction accounts for just under half of all industry jobs, and 3D-printed homes might make a dent and help companies do more with fewer employees. The construction industry faces a steep labor shortage: There were 300,000 to 400,000 open jobs in the sector in the fall of 2021, according to the Home Builder Institute. “Owners can also choose to preserve the look of the layered 3D-printed lines or have an accent wall in places.” Meeting demand “The inside of the home can look very similar to traditional houses in that you can just plaster the wall for a nice flat look,” says Kristen Henry, chief technology officer at SQ4D. Once complete, the houses can be customized on the inside. Workers construct the remaining components, such as the roof and rebar, for structural reinforcement and integrity. Construction company SQ4D, which built the Riverhead home, also prints the concrete foundation. The additive manufacturing process usually prints the interior and exterior walls of the house and utility conduits. As a new layer of concrete is added, the older one cures. Rendering by SQ4D.ģD printing a home follows these same basic principles: A printhead, operating on a gantry, moves back and forth along a fixed and prescribed track and deposits concrete or other materials of choice layer by layer. Because the process adds material systematically, it is also called “additive” manufacturing. A printer then follows these instructions to construct a 3D equivalent of the designed object by depositing or extruding material layer by layer. But a Riverhead, New York, home made news in 2021 for one special reason: It was primarily constructed by a 3D printer.ģD printing involves digitally designing an object and creating build instructions on a digital file. Under ordinary circumstances, a three-bedroom, two-bath house hitting the market would not have landed headlines. Teile und Upgrades der Enterprise-Klasse.Lizenzen und Usage Intelligence managen.Workstations mit künstlicher Intelligenz.Alle Lösungen für die Arbeitswelt anzeigen.Energie, Klimaschutz und Nachhaltigkeit.Cloud-Lösungen für unstrukturierte Daten.PowerSwitch-Campus-/Zweigstellenswitche.Storage-Automatisierung und Entwicklerressourcen.Moderner Storage für Kubernetes und Container.Lösungen für die Microsoft Azure Stack-Produktreihe.Alle Lösungen für hyperkonvergente Infrastruktur anzeigen.Alle APEX Cloud Services-Lösungen anzeigen.
